Embroidery, as a process, goes back thousands of years. The earliest recorded embroidered garment dates back to 700 CE. Today, the embroidery process is completely digitized, though some of the foundations of embroidery are still key to the process as a whole.
Old Tools
-Hoop
The use of the embroider hoop dates back to the beginning of the process. They were originally made of wood, bone or ivory. Today, they are made of wood or plastic. Even machines with multiple stations still require one hoop per station. Hoops are necessary to keep the fabric taut while working.
-Fabric
Thread or yarn is used in the embroidery process. Modern commercial embroidery thread is most often made of cotton or rayon, and available in unlimited color combinations.
New Tools
-Computer design
“In 1980, Wilcom introduced the first computer graphics embroidery design system to run on a minicomputer. “
The ability to design a multi-colored image has come a long way, but it still the hardest art to set-up because it requires the highest minimum font sizes. Detail is limited because in embroidery you are using thread instead of ink, and are confined by the size of the thread.
-Computer machinery
Current embroidery machinery can run more than 55 heads at once with more than 25 colors at one time. Tajima and Barudan are two top embroidery machine manufacturers.
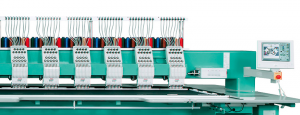
Photo from Tajima
Method
-Process
The age-old process of pulling the fabric tight, setting it into a hoop and stitching into it, remains the same. However, the types of fabric and the speed of which determines the length of the process. The average logo contains approx. 8,000 stitches or less.
-Material
Embroidery is a sturdier, more substantial imprint process than screen-printing. You can embroider on most fabrics, from cotton to blends to full polyester or rayon. The favorite location for apparel, and the spot that receives the most impressions, is the front, left chest.
Embroidery remains the second most popular imprint method for promotional apparel. The ability to customize embroider on a bucket hat or a polo shirt, a soft-side cooler or picnic blanket, allows the customer to be flexible in the promotional product choice, even when limited by design. Click for more information on other imprint methods. Contact us for more information about your logo and how we can embroider it on just about anything!